At work, we’ve been playing around with 3D printing services, namely the international chain or distributor known as Hubs. A coworker described it very accurately as “the uber of 3d printing services” where people that have access to printers apply for certification, and people who don’t place an order on Hubs which then distributes the workload among the certified people with the equipment. Kinda cool, but there are weirdnesses.
Specifically, of the five separate designs I’ve placed in the past two years, about half of those have been good, solid parts, and the other half have cracked and broken with varying degrees of damage and recovery methods.
I figure this can be my own reference on “what I consider a functional print method and functional material for something more than a mechanical prototype.
The three print methods we’ve used so far are probably the three most common: FDM, SLA and SLS.
FDM – Hot Glue Gun
Melt a plastic filament in layers over a baseplate and build the model up layer by layer.
SLA – Liquid and Lasers
Built from the top down, from what I understand a UV laser …basically cauterizes a liquid resin at certain points on the liquid surface. The vat sinks and the solid model emerges layer by layer, stuck to the underside of the baseplate.
SLS – Laser-Blasting Powdered Plastic
From what I’ve read, a UV laser fires into a bed of powderized plastic, melts and resolidifies its surface in very small places and the solid emerges layer by layer
I’ve created orders with Hubs for 4 different combinations of methods and materials:
- Duraform PA – SLS
- HP 3D High Reusability PA 12 – SLS
- ABS-Like Tough Resin – SLA/DLP
- ABS – FDM
The Duraform PA nylon part that I had made was VERY thin-walled. It built up nicely but due to a <0.7mm wall, it cracked with very little strain. A second part that formed around this was super solid, though. So as long as my wall thickness was > 1.0 mm, I had no problems with it.
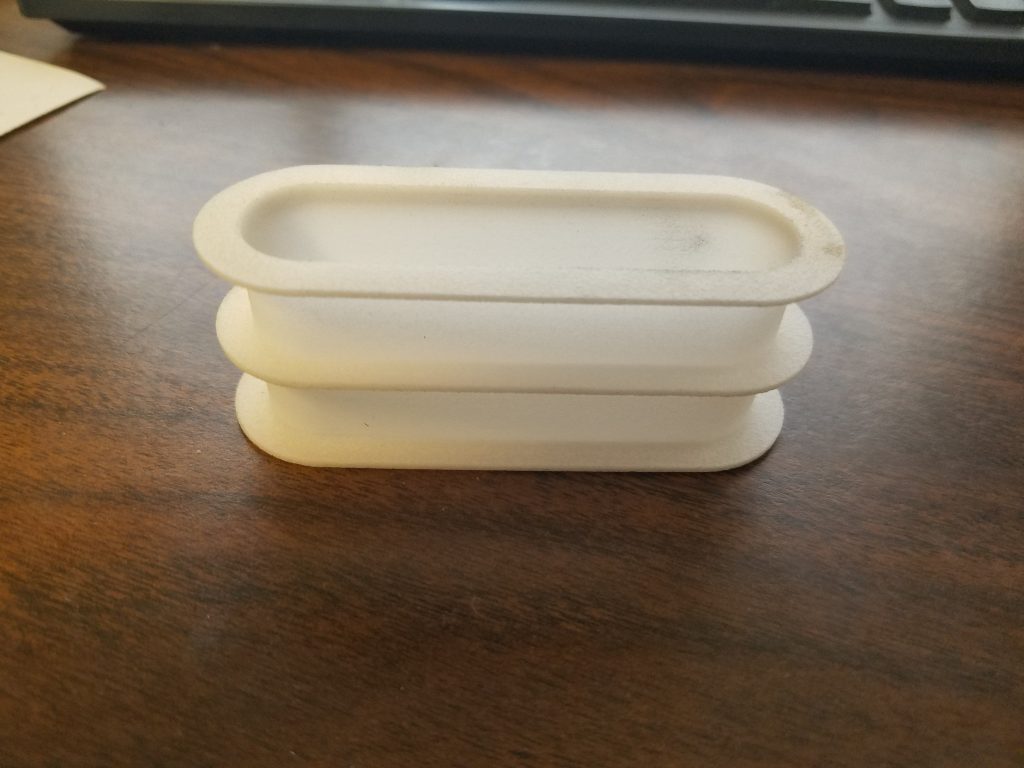
That and a few design changes required that I reprint a revision of the first part with PA 12 nylon with a minimum of 1mm wall thickness. This was VERY good quality in comparison with the first revision. Like the Duraform, it was structurally sound, and as I maintained a minimum wall thickness, I had no problem with it. The only oddity that I didn’t like about it was its grainy texture and unrefined feel. But it does mill nicely afterwards.
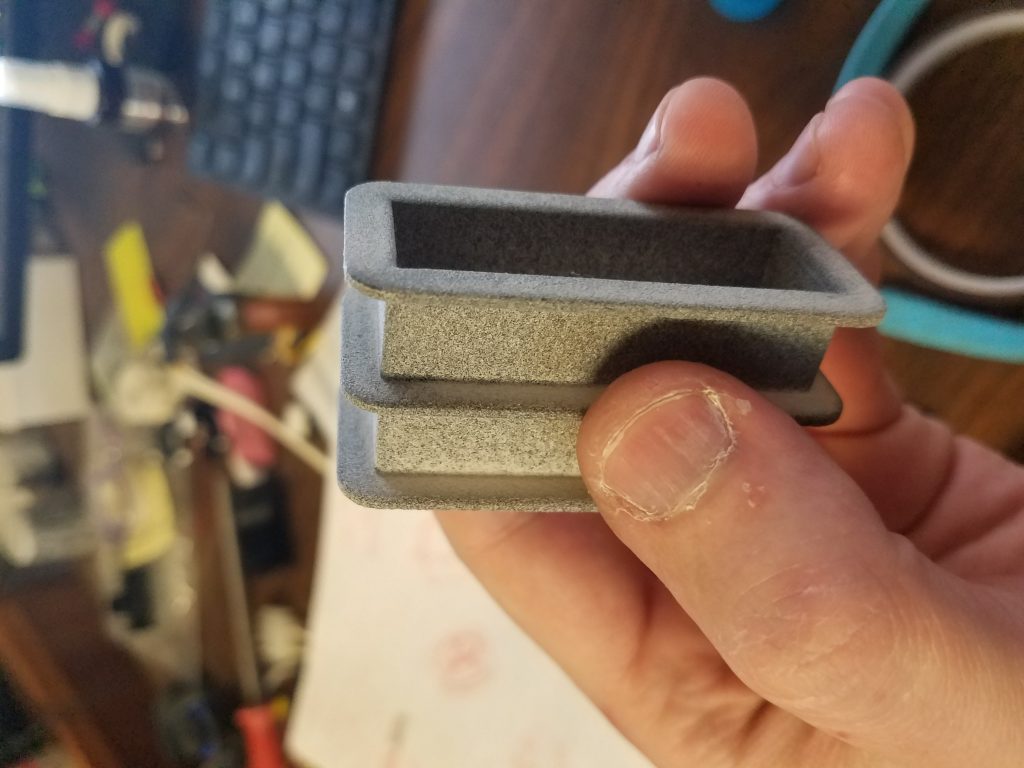
A year has elapsed, and in the past two weeks I’ve been ordering new parts for a new project. Not remembering what we used before, I started the choice from scratch. That and Hubs overhauled their entire interface, anonymizing the vendor experience, and making it a LOT easier to pick and choose materials along with automatic costing and such. As such, the first material we ordered was “ABS-Like Tough Resin”. I didn’t know what SLA meant at the time (with its liquid factor and all), but now it makes sense and really acts nicely, save for the springy feel and tendency to peel and wrinkle with any lateral pressure such as scraping it with a penknife.
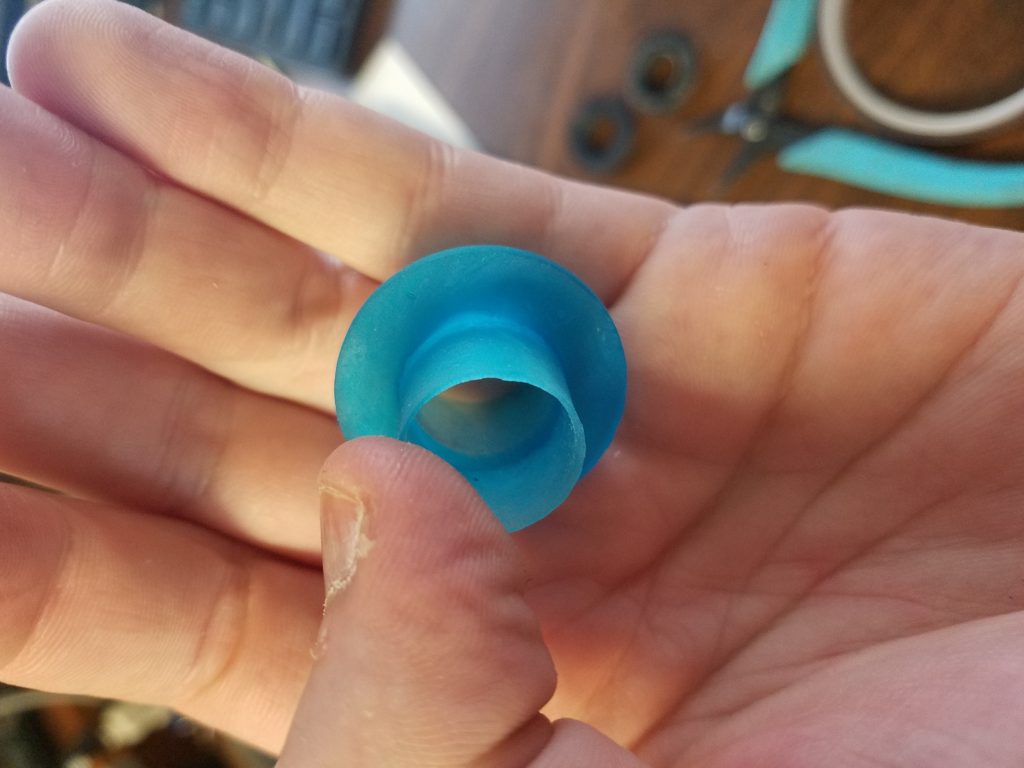
The final method we’ve been using (and having the least amount of success with) is straight ABS using the FDM process. The layers here are clearly evident, and even their structural stability is super easy to balk at, as any little pressure in a weak spot “delaminates” the part. Plus the finish is messy and not ideal to work with. But we figure we can still make the parts we have work without needing to re-order them in a different process and material
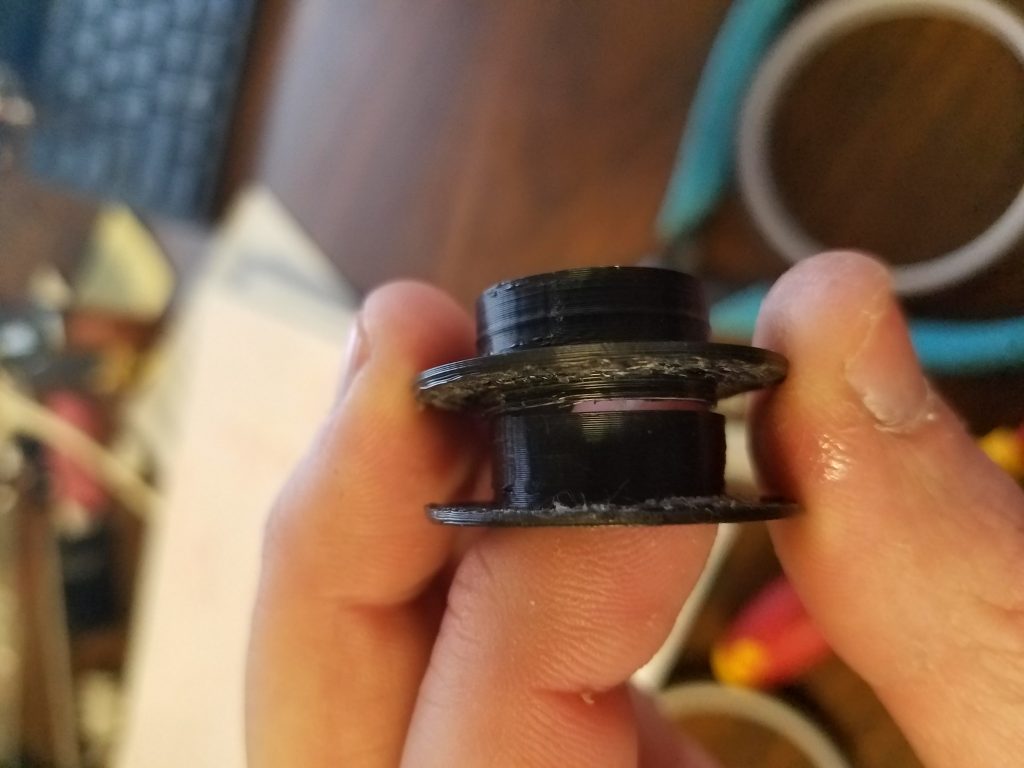
Now I HAVE been toying around with the idea of getting a printer for the shop (or more for myself with a loan policy).
From what I see, though, FDM printers run anywhere from $200 to ..reasonably expensive, and are dependent mostly on cubic volume you have to make a part. Filament is about $20 a kg. Between price, volume and ratings, I have my eye on the Creality Ender 3 Pro (approximately 8 cubic inch volume) for $260.
SLS printers are the MOST expensive of these three. A number of factory-direct models are well over $10k. Based on price and technology, I’m GUESSING this is the laserjet of 3d printers. And Amazon’s selection of jars of “Sinterit Powder” is quite pricey too. I’m not even considering this as a viable purchase for personal use.
SLA printers seem to be in the middle, price-wise, with the smallest at $150 (4.75″ x 2.5″ x 5.5″), a good median of $500 or so, and bigger models no less than $1000. Like FDM, SLA resin is around $40-$50 a kg bottle. From what I see on Amazon, my best bet, knowing that the above dimensions is going to be an ANYCUBIC Photon or ELEGOO Mars (each giving me the above working volume) for $400-$429.
All this to say: I have no idea what I’m doing here. I’m really displeased with the FDM process. Seeing how these parts turned out has really discouraged me from buying even a cheap Monoprice, despite the reviews on Amazon. However, the prospect of making something like this work is very attractive, and if I can save up for something that would give me a better quality part, whether it’s a toy or a D&D figurine model bought on HeroForge, or whatever, I would totally do it. But it’ll DEFINITELY be one of those things I research the heck out of before I hit “buy now.”
Leave a Reply
You must be logged in to post a comment.